NEW AGRICULTURAL MAINTENANCE SHOP FEATURES GEOTHERMAL, SOLAR
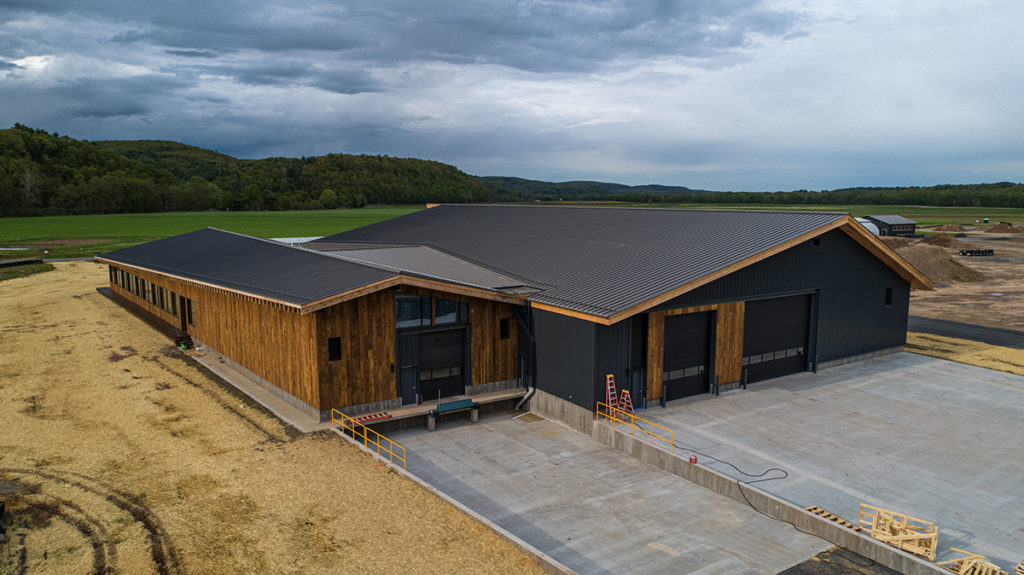
Drive south on Hurley Mountain Road and look to your left and — depending on the time of day — you might see the outline of a new building on the farmscape. The structure’s standing seam steel roof glistens below the moving clouds. This is not your typical farm shed. Look closer and you will see that the construction is actually two buildings at different scales and distinct but complementary material palettes, unified beneath a conjoined, double gable roof.
The Farm Hub has completed construction of a new facility that will house farm equipment including tractors, combines, machine parts and office space for the production team. The machine shop, or “the shop” for short, is a result of years of planning as the Farm Hub continues into its next phase of growth.
The roughly 27,000 square-foot building has a vaulted ceiling and tall overhead doors to accommodate large equipment, and a spacious open floor plan for productive work, maintenance and instruction. The new space, which replaces the current single bay machine shop, is designed for work on multiple pieces of farm equipment simultaneously and features a large storage area for tractor supplies and parts. The adjoining office and meeting space is intended for farm operations staff.
Functionality and practicality were non-negotiable when it came to the project. Design and environmental considerations were also paramount. The exciting challenge was to envision a contemporary 21st century farm building, with careful attention to how the building would relate to the farmscape and create harmony between the architecture and its natural surroundings. The design team strove to unlock harmonies between the vernacular agricultural building form and a more contemporary aesthetic, and between the industrial and human scale – both inside and outside.

Being very sensitive to the size of the building, Christopher Kroner refers to the conjoined buildings as “a mother and child of sorts; a strategy for mitigating between the intimate human scale and the industrial scale of the equipment,” he says.
The Hurley Mountain flats provided an inspiration and backdrop for the double gable which calls to mind the shape of the mountains in the distance.
“The double gable introduces a dialogue with the landscape of the mountains beyond, and helps balance the human scale of the offices and the industrial size of the shop,” Kroner adds.
From its inception, the shop was designed and constructed with sustainability at the forefront.
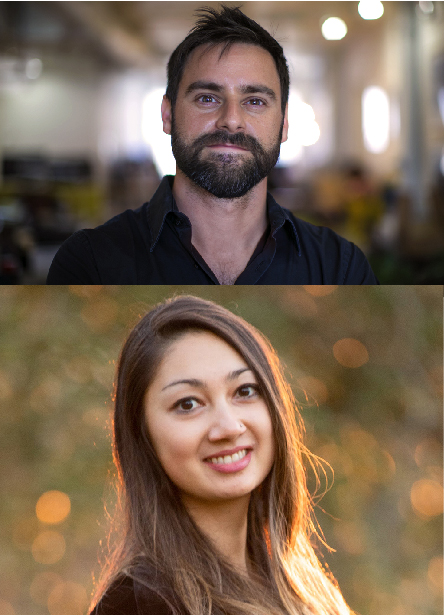
In 2017, the Farm Hub hired MASS Design Group, an international architectural firm with a Hudson Valley office, for the job. MASS is no stranger to design that celebrates sustainability: similar projects include the Rwanda Institute for Conservation Agriculture and the Ellen DeGeneres Campus of the Dian Fossey Gorilla Fund. MASS’s Christopher Kroner, Principal, and Evelina Knodel, Associate Designer, led the initiative.
The goal from the start was “to create the most sustainable facility that we could and working to create net zero, if not net positive infrastructure for the Farm,” says Kroner. Geothermal heating and cooling systems, a large roof-mounted solar array, an efficient building envelope, specialized glass designed to minimize bird collisions, and reclaimed materials are among the solutions settled on by the Farm Hub and MASS Design Group teams over the course of the design process.
Site Planning
Pinpointing the building’s location on the site required synthesizing multiple information layers, including soil quality, prime agricultural land, flood zones, wildlife habitat and riparian edges, solar orientation, windrows, viewshed, and site circulation. The team also had to take into consideration the farm’s location within the Federal Emergency Management Agency (FEMA) 100 year flood plain and the regulations that go along with the designation.
Kroner says: “Ultimately we were able to identify a location that had enough elevation rise, not enough to get out of the flood plain, but outside of the zones pointed out to us by staff that flood badly during heavy storms.”
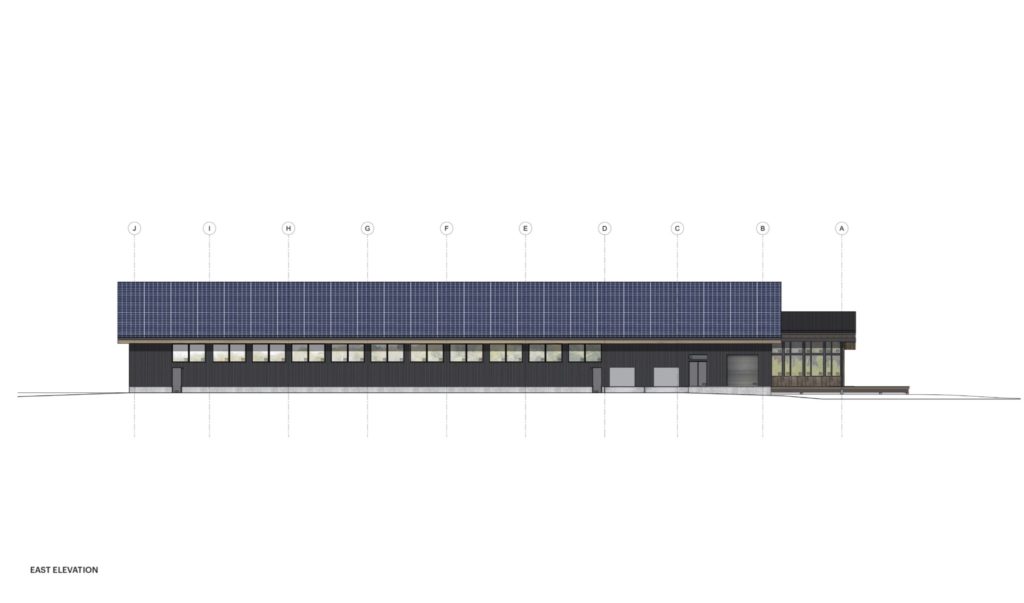
Shadow studies using modeling software simulated the shadows cast by the building and the adjacent Hurley Mountain at different times of the day and year. This process ensured that the new structure would not block any solar heat gain potential for the nearby greenhouses. It was evident that an east-west axis would maximize exposure for the solar array, capturing the maximum sunlight for solar energy and funneling light to the greenhouses for the “best growing capacity,” Knodel says.
Now, solar panels cover the eastern roof leaf of the building, expected to produce around 170,000 kWh (kilowatt hours) of energy each year. Solar energy, in conjunction with the geothermal system, will almost completely offset the energy demand of the building. “The motivation was to create as much clean energy as possible,” says Derrick Doubrava, the Farm Hub’s construction and facilities manager.
Geothermal
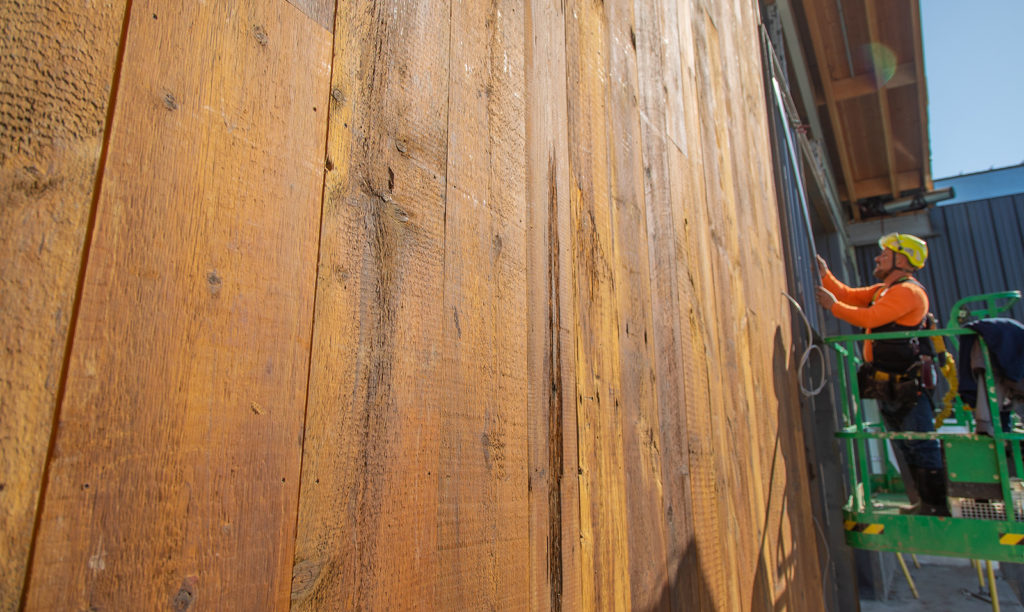
The building uses geothermal for both heating and cooling. Employing a series of wells and pipes that run nearly 500 feet deep, the system taps into and extracts the natural temperature of the earth and disseminates it throughout the building. “This is significant in terms of efficiency for a building of this size,” says Doubrava. To preserve heat during winter and boost cooling in the summer months, high quality roll-up doors to provide maximum insulation were installed.
All of the siding on the office side of the building is reclaimed wood, while the shop itself is constructed with metal siding in charcoal grey. The design team worked with Excelsior Wood Products, a supplier in Kingston, NY to procure the reclaimed lumber.
Insulation + Longevity
The durable, standing seam steel clad roof is well insulated for a long lifespan. The floors throughout both the shop and the offices are concrete, providing a durable and easily cleanable surface. On the office side, the floor is coated in concrete densifier for the office floors. Rockwool insulation, a natural alternative to traditional batt insulation, was used to fill the wall cavities on the office side of the building. This serves as both a thermal efficiency measure as well as an acoustic absorber for the offices.
LEED Certification
The Shop is on track to receive LEED Silver Certification. Overseen by the U.S. Green Building Council, LEED certification means that a building meets a checklist of standards for sustainability, thereby receiving “green building” status. Successful certification also involves a checklist of standards for interior design and construction. Silver status means that a higher than baseline level of energy efficiency has been achieved.
The Enjoyment Factor
Perhaps one of Kroner’s favorite features is the porch at the northern entrance. During the planning phase he observed that staff would often congregate outdoors or at various buildings to talk or share meals. The theme of community, and everyone’s desire to spend time outdoors, inspired the porch that extends out towards the landscape between the kitchen and meeting room and wraps around the front and west sides of the building.
“During the (pre-pandemic) discovery phase we saw how staff and collaborators valued the ability to gather and socialize outdoors,” says Kroner, talking about the inspiration for the wrap-around porch, where people can congregate but remain protected against the elements.
Finally, beyond the practical, the innovative, and the sustainable lives the idea that staff and visitors will simply enjoy the hub of activities around the building whether in the office, the conference room, or on the porch.
“The design is meant to generate excitement that is very easy to feel the energy of what’s happening in the shop without being in the action,” Kroner says.
-Amy Wu
References:
The Many Uses of Farm Buildings by George Wanamaker, farmcollector.com
Barns- Functions & Forms by Bill Ganzel, livinghistoryfarm.org